How to deal with air bubbles generated by polyurethane encap
There are two sources of bubbles:
1. The components react with a small amount of water to generate carbon dioxide;
2. Air is brought into the stirring process.
It is much better to use pouring with vacuum, and the key point is to close the mold at the gel point and use pressure to expel the air in the polyurethane encapsulation system.
1. Stirring: Pour the liquid material into the container first, then slowly add the powder material, and at the same time fully stir for 3-5 minutes to form a uniform slurry without raw powder masses and particles, and then use (a mixer is best) .
2. Brushing: Brush directly on the base surface with a brush or roller brush, using even strength, and do not miss the brush; generally it needs to be brushed twice (according to the requirements of use), and the thickness of each brushing should not exceed 1mm; The first time is slightly dry and then the next painting (just not sticky, usually 1-2 hours apart), two vertical and cross paintings, the total thickness of the painting is generally 1-2mm; if the coating has been cured , Moisten with water before applying another layer.
3. Curing: It is recommended to cover the coating with a damp cloth or spray water to maintain the coating 24 hours after construction.
4. Protection: Please take protection against trampling, rain, sun exposure, sharp damage, etc. before being completely dried after construction.
5. Inspection (closed water test): After the waterproof layer is dry (at least 24 hours in summer, at least 48 hours in winter), please store full water for 48 hours to check whether the waterproof construction is qualified.
The volatile matter mainly comes from the environment. On the one hand: the moisture in the environment will be adsorbed in the filler to generate volatile matter. Among them, the most likely source of moisture is the filler. Fillers such as clay, carbon black and silica have strong Water absorption, especially the water absorption of liquid-phase white carbon black can be as high as 10% by mass; on the other hand: when the rubber compound is mixed, billeted, injected and flowed, it will be inhaled or drawn into the processing machinery and will become volatile. Copies.
1. The components react with a small amount of water to generate carbon dioxide;
2. Air is brought into the stirring process.
It is much better to use pouring with vacuum, and the key point is to close the mold at the gel point and use pressure to expel the air in the polyurethane encapsulation system.
1. Stirring: Pour the liquid material into the container first, then slowly add the powder material, and at the same time fully stir for 3-5 minutes to form a uniform slurry without raw powder masses and particles, and then use (a mixer is best) .
2. Brushing: Brush directly on the base surface with a brush or roller brush, using even strength, and do not miss the brush; generally it needs to be brushed twice (according to the requirements of use), and the thickness of each brushing should not exceed 1mm; The first time is slightly dry and then the next painting (just not sticky, usually 1-2 hours apart), two vertical and cross paintings, the total thickness of the painting is generally 1-2mm; if the coating has been cured , Moisten with water before applying another layer.
3. Curing: It is recommended to cover the coating with a damp cloth or spray water to maintain the coating 24 hours after construction.
4. Protection: Please take protection against trampling, rain, sun exposure, sharp damage, etc. before being completely dried after construction.
5. Inspection (closed water test): After the waterproof layer is dry (at least 24 hours in summer, at least 48 hours in winter), please store full water for 48 hours to check whether the waterproof construction is qualified.
The volatile matter mainly comes from the environment. On the one hand: the moisture in the environment will be adsorbed in the filler to generate volatile matter. Among them, the most likely source of moisture is the filler. Fillers such as clay, carbon black and silica have strong Water absorption, especially the water absorption of liquid-phase white carbon black can be as high as 10% by mass; on the other hand: when the rubber compound is mixed, billeted, injected and flowed, it will be inhaled or drawn into the processing machinery and will become volatile. Copies.
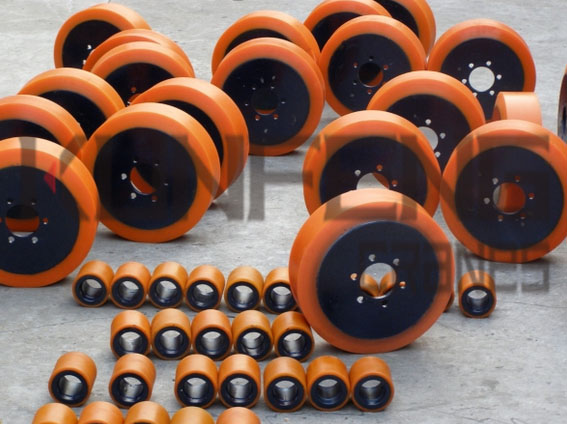